Abrasion in Refractory
Articles
Wear is defined as damaging gradual removal or deformation of material at solid surfaces. On a chemical basis, wear is called corrosion. In mechanical terms, wear is erosion, or more specifically abrasion.
Abrasion is defined as the loss of material that occurs when hard particles, also called abrasives, are forced against and move along a solid surface. The notion that abrasion is a loss is important to remember here, as it will also define the testing for abrasion resistance.
Early in its history, Resco was confronted with abrasion challenges while it was serving the petroleum refining industry just after World War 2. It was at this time that technology for the Fluid Catalytic Cracking Unit abbreviated the FCCU, and was being perfected.
The FCCU is a pair of furnaces that are pressure vessels. One vessel is called the reactor in which gasoline is made by cracking crude oil. A fine, but abrasive, alumina catalyst is used for the cracking reaction.
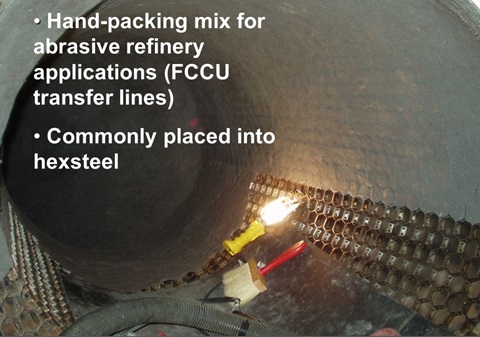
The second vessel is the regenerator in which carbon that is deposited on the catalyst is burned off, regenerating the catalyst. Inside the vessels are refractory-lined cyclones that remove the catalyst from the gas stream. Between the two vessels are transfer lines that convey the catalyst. The vessels operate at about 1500°F, so the transfer lines have to be refractory lined. The refractory must be abrasion resistant to survive
the 5 to 8-year campaign between FCCU repairs.
Resco’s most famous product is RESCOBOND AA-22S, which is the abrasion-resistant hard refractory castable that protects the transfer lines. The photo shows an installation of AA-22S in a transfer line. AA-22S is commonly placed into the hex-steel mesh for both the transfer lines and the vessel cyclone linings, and it is known the world over.
Testing for Abrasion Resistance
The test procedure sprang from the developmental days of the FCCU vessel. The method attempted to simulate a fine abrasive flowing through a duct at high velocity scratching the refractory. The exterior photograph shows the feed system for the abrasive, which is 1,000 grams of No. 36 silicon carbide grit. Recall that silicon carbide is a 9, just below diamond in the Mohs scale. A venturi device is used to control the flow so that the test runs for 450 seconds. A 65-psi dry air supply propels the grit against a target. The pressure inside the box is relieved through a simple dust collector.
Inside the box is a glass tube nozzle that directs the silicon carbide grit. The grit is propelled against a target which is a 4” x 4” x 1” thick plate of refractory. If the specimen is a brick piece, the sample is just dried before testing. If the specimen is a castable, the sample is dried then heated to 1500°F for 5 hours, cooled, and then tested. The initial weight of the specimen and its density is accurately recorded.
The abrasive cuts a round cavity into the specimen. After the test, the final weight of the specimen is recorded, and the volume of the cavity is calculated from the measured density. The results are expressed as cubic centimeters of lost volume. Less resistant materials have high weight loss, so a large number is bad. A small number of abrasion loss is good.
Below left is a photograph of a C-704 test plate of a material that had poor abrasion resistance. You can see the grit cut a hole completely through the specimen.
Evaluating the Severity of Abrasive Conditions in an Industrial Furnace
What are the conditions that cause abrasive wear? Obviously, there must be a motion of particles over a refractory surface. The abrasive particles must be forced against the surface. The force may be gravity or a high-velocity gas stream carrying dust. The force can also be the weight of the limestone charge in a rotary kiln. The particles likely will be harder than the refractory surface, but that is not always the case. And larger particles, like the limestone feed to a rotary kiln, will cut faster and deeper than finer particles.
An everyday example of abrasive wear is the removal of a rust spot from the body of a vehicle with a sanding disc. We can select alumina sandpaper for the abrasive medium on the disc. Alumina is also called corundum and has a Mohs hardness of 9. Remember steel has a Mohs hardness of 4. If you are trying to remove a lot of rust, use a coarse grade of sandpaper. Now equations for abrasion have been developed, and two of the more important parameters include the force applied and the velocity of the abrasive particles. When sanding, the more force applied to the disc, the greater the amount of rust removed. The faster the disc is rotating, that is, the higher the angular velocity, rust is removed more quickly.
A simple rating index can be devised to describe the severity of the abrasion. Do not confuse this rating system with the cc-loss result of an abrasion test. A high abrasion severity index for an application or condition will require a LOW cc-loss refractory. In rating the application, a + sign indicates the condition is present. A ++ indicates a more extreme condition. A ½ indicates the condition is present but mild. A zero indicates the condition is not a significant factor for abrasion.
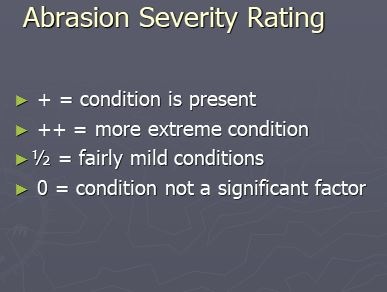
This can be applied to an industrial application, using the rotary lime kiln process as an example.
Abrasion in a Lime Kiln Transfer Chute Refractory Lining
The lime industry uses a refractory-lined vessel called a stone preheater to improve kiln efficiency. The transfer chute is the breeching between the stone preheater, up and above, and the rotary kiln, below. During operation, rams or pushers shove the limestone off the preheater floor causing the stone to fall through the hopper onto the refractory in the transfer chute, as shown by the gray dots represent the stone in this sketch below. The gas flow is represented by the red arrows.
Monolithic refractories designed for abrasive conditions
As a matter of review, refractory concretes/castables are blends of refractory aggregates in a bonding matrix. The matrix includes the cement binder as well as admixtures and fillers that reduce water requirements and other ingredients to control set and flow.
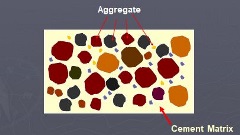
Good attachment between the binder and the aggregate, or in chemical terms, good intermolecular bonds. We touched on phosphate-bonded refractories earlier, and good intermolecular attachment is a characteristic of the alumina-phosphate bond, so it is not surprising that phosphate-bonded alumina bricks have great abrasion resistance.
The plate on the right shows a typical result of an ASTM C-704 test on a conventional, high-cement content 40% alumina fireclay castable. A fairly large cavity was eroded by the grit.
Note that the aggregate was not standing very proud, with the aggregate and the cement matrix about evenly eroded, giving a value of 20 cc’s loss.
Let’s evaluate castables with more abrasion-resistant aggregates than 40% alumina fireclay. We’ll select corundum with a Mohs hardness of 9 and then follow up with silicon carbide at about 9.5 Mohs hardness.
This is the specimen plate of tabular alumina, also known as corundum, a
high-cement content conventional castable. This material is widely recognized as having abrasion resistant properties.
R-Max extreme service products
R-MAX products were developed by Resco for its petroleum refinery market. The technology features abrasion-resistant aggregates in an extremely strong matrix. We have developed a variety of compositions for mineral processing applications in the R-MAX product family.
Our general service R-MAX products are listed here. The C suffix indicates a casting-only material. A G suffix indicates that that product is only suitable for gunning. Note that the abrasion test numbers are higher for the gunning mixes. This is because we do the abrasion plates by casting in the lab. These gunning mixes cast poorly in the laboratory and require more water than casting grades, which yields more abrasion in the C-704 test. We expect that the abrasion resistance of a gunned R-MAX lining will be better than what the cast sample laboratory tests indicate. The QT suffix indicates that the product contains QUIKTURN technology for fast dry outs. PC suffixes indicate pump casting grades, also useful for shotcrete linings.
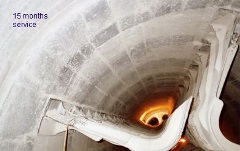
The two photos below show one of the first R-MAX linings in a long rotary pebble lime kiln, the extreme feed end in a heat exchanger zone. Remember the heat exchanger location gets my most severe abrasion rating at a 6. After 15 months the lining looked great, a bit polished, and you can easily see the marks from the form boards. This lining was vibration cast at between 4.5% to 5% water using R-MAX C.
After 27 months, the same lining is still in great shape, although the cold joints at the edges of the pours are more pronounced. This lining is ready to give several more years of service.
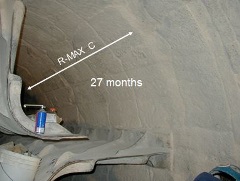
The R-MAX PC QT in this case was cast at a lower 5% water, typical for vibration casting. Visually you can see the importance of water content for abrasion resistance.