Adding Spinels to Magnesia Brick
Articles
A combination of four articles will go over magnesium the element and the production of magnesia refractory products. This is Part 4: Magnesia with Various Spinels
Part 1 Magnesium the Element
Part 2: Subtle role of Calcium in Magnesia Refractories
Part 3: Magnesium Oxide Refractories
Spinels are minerals that are combinations of divalent and trivalent metal oxides in a cubic crystal formation. There are a number of naturally occurring spinels. The divalent metals are iron II oxide or magnesia. The trivalent oxides are iron oxide, alumina, and chrome.
Spinels used in Refractory:
- Magnesia-alumina spinel
- Chrome ore - an iron II oxide -chromia spinel
- Hercynite spinel
Hercynite is a divalent iron aluminate spinel, and also will be a topic for a future time. We will take the easiest spinel first, magnesia-alumina.
Many magnesia-spinel bricks used in rotary lime and cement kilns are binary combinations of refractory magnesia, DBM, and synthetic magnesia-alumina spinel. Magnesia-spinel bricks are primarily magnesia bricks, with some spinel added. This shows the approximate proportion of magnesia to spinel in an 85% MgO spinel brick. You can see the magnesia far outweighs the spinel component.
Effects of adding Spinel to Magnesia Brick
When brick makers add spinel to a magnesia brick, there are numerous benefits in terms of physical properties. Spinels decrease the thermal expansion rate of magnesia brick. A refractory with high rates of reversible thermal expansion have poor thermal shock resistance. Spalling results from stresses that occur in hot refractory that have unequal rates of thermal expansion or contraction.
Refractories that have very high rates of thermal expansion are prone to cracking and spalling. Compared to magnesia, spinels have lower rates of thermal expansion. The addition of spinels improves the spalling resistance of magnesia brick. Finally, spinel has a lower thermal conductivity than magnesia. The addition of spinel to a magnesia brick proportionately reduces its thermal conductivity.
Magnesia brick that contains 20% magnesia-alumina spinel is going to be a better insulator than one that contains only 10% spinel. In a rotary kiln operation, that translates directly to lower kiln shell temperatures.
Resco offers three primary magnesia-spinel bricks, RESCOMAG’s 85-C, 92 FMS, and 85 FMS. These products are used in rotary cement and lime kilns. Decoding the suffixes, the numbers 85 and 92 stands for the approximate magnesia content. Dash C means the product is made in China right now. FMS stands for fused magnesia and fused spinel.
Primary Magnesia-Spinel Bricks:
- RESCOMAG 85-C is a magnesia-spinel brick made from DBM (sintered magnesia) and contains about 85% MgO.
- RESCOMAG 92 FMS has higher magnesia content and contains both fused magnesia and fused spinel. RESCOMAG 92 FMS is for high wear applications. Typically, magnesia-spinel refractories have bulk densities in the 180 pcf range.
This table lists the chemical analysis of two of our brands, RESCOMAG 85-C and RESCOMAG 92 FMS. The alumina content of the brands is dependent on the amount of spinel. Multiply the alumina by 1.5 and you have the approximate spinel content of the magnesia-spinel refractory. The spinel content may help you understand cost differences. Spinel is usually the most costly of the two common ingredients, DBM, and synthetic spinel.
Two other notes: spinel bricks that normally do well in cement and lime kilns have higher lime to silica ratios, at least 1.5:1. Second note: when you have magnesia, lime, silica, and alumina in a brick composition, eutectics can form with melting temperatures as low as 2490°F. In order to keep the amount of liquid low in a magnesia-spinel refractory, the total lime and silica must also be low.
Magnesia Chrome Spinel
Chromite, a more complex spinel is often called chrome ore. Chromite is a naturally occurring mineral, found in a few locations around the world. The most commonly known refractory chromite is South African chrome ore. Chromite is primarily a divalent iron-chrome spinel, although the mineral has quantities of magnesia, trivalent iron oxide, and alumina.
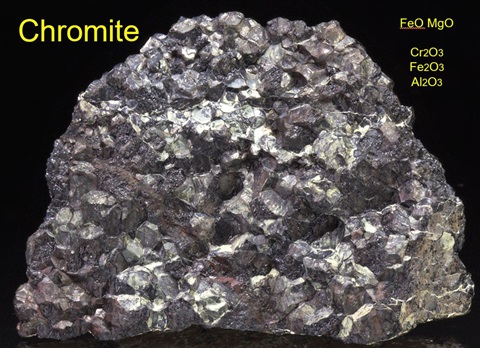
Why chrome is so valuable in smelting furnaces is explained in this phase diagram. The X-axis represents the % chromic oxide in a binary mix of silica and chromic oxide. The Y-axis is the temperature in degrees C. Silica readily melts at about 3100°F. The yellow shading shows the region where both chromic oxide and silica are liquid. This does not occur below 2250°C (4,082°F). This means that molten silica and solid chromic oxide are not miscible below 4000°F. Thus, chrome bearing refractories have resistance to wetting by molten silica slags at furnace operating temperatures.
The magnesia-chrome technology matured into three varieties of brick: silicate-bonded, direct-bonded – vintage 1960’s-and fused grain brick.
The Benefit of Adding Chromite to Magnesia Brick
First, magnesia and chrome ore undergoes a lot of solid-state diffusions when a refractory brick is going through the firing stage in a tunnel kiln. During the firing of a brick that contains chromite, MgO reacts with chrome ore. The reaction forms magnesio-chromite and magnesio-ferrite, two highly refractory spinels.
Second, the silicates that are associated with chrome ore have low temperatures of initial melting. If you manufacture a chrome ore brick, it will take only a very low firing temperature. The melting silicates would cause the pressed bricks to stick together if they were over fired. Adding magnesia to a chrome brick converts the silicate to fosterite, which as you recall, is very refractory, according to the lower equation. This lets you fire the brick at a much higher temperature to improve physical properties.
This is a typical chemical analysis of South African chrome ore. Chrome oxide is the primary constituent, although there is plenty of iron oxide and alumina, too. One feature of South African chrome ores is their low silica content.
Silicate-bonded magnesia chrome bricks take low firing temperatures and have high silica contents. Early magnesia-chrome compositions were based on Philippine chrome ore, which contained a lot of silica. Plus, the commercial brick-making magnesia available at the time was fairly low purity and contributed to the silica content. This first generation of mag-chrome brick was used early on in steel furnace applications, although higher-quality mag-chrome products eventually superseded them.
Today, silicate-bonded mag-chrome bricks are used in non-ferrous metal refining, where you want a high content of chrome. It can also be found in glass tank regenerator checkers where these products are favored for their lower cost, high density, and heat capacity. Heat capacity, the ability to store heat, is an important property in glass furnace regenerators.
CRB 20-C is an example of a silicate-bonded magnesia-chrome brick. Note the high density at 194 PCF, almost 5% total lime + silica, and a nice, high chrome content of 27%.
The advent of high purity synthetic refractory magnesia, low in silica, brought about the technology of direct-bonded brick. Proper selection of chrome ore allowed very high firing temperatures well above 3000°F.
In fact, some Japanese manufacturers of magnesia-chrome brick for cement kiln burning zones reportedly fired their brick near 3300°F.
The high firing temperatures create a special microscopic feature in direct-bonded brick, which is the direct attachment of the magnesia grains to the chromite grains. This direct intergranular attachment gave the bricks high hot strength and very good spalling resistance. 60% of magnesia bricks became the most popular. Although 80% of bricks were used in many cement kiln applications.
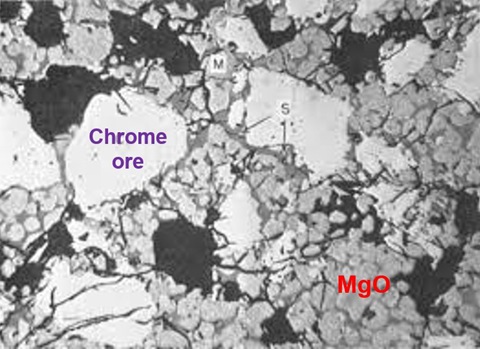
Resco offers several direct bonded bricks, including NUCON 60-C and KRILEX 50-C. Metallurgical applications for this second generation of magnesia-chrome brick include AOD vessels, lead, copper, cobalt/nickel, and platinum group metal furnaces and steel degassers.
This data are for NUCON 60-C, our most popular direct-bonded brand. It features high density, low total lime + silica, and 17% chromium oxide.
Magnesia-Chrome Re-Bonded Fused Grain Brick
The final development in magnesia-chrome technology was the re-bonded fused grain brick. This refractory type was brought into the market in the late 1960s. It was an improvement over direct-bonded brick for slag resistance in metallurgical applications. The starting materials are magnesia and chrome ore that are melted together in an electric furnace at extremely high temperatures. The melt is cast into ingots, which are milled after cooling into sized brick-making fractions.
Fused grain bricks feature low porosity and superior slag resistance, as the chrome is well dispersed throughout the granular raw materials. Some direct-bonded brick compositions utilize partial additions of fused grain while other brick brands are composed 100% of fused grain. Because fused grain production is very energy-intensive, fused grain brick is more expensive.
This table lists Resco’s direct-bonded magnesia-chrome offerings. Two of our more popular fused grain brands include KRILEX 621-2-C, which exhibits great wear resistance for its cost. The second most popular fused grain brand is GRFG which is 100% fused grain.
Magnesia Conclusion
Virtually all basic refractories today contain magnesia. Magnesia is the refractory material of choice for metallurgical and steel production furnaces and cement and lime kilns.
Characteristics of Magnesia Brick
- High melting temperatures
- High resistance to iron oxide
- Absorbs divalent iron oxide
- Excellent alkali resistance
- High rates of reversible thermal expansion & thermal conductivity
Magnesia is combined with various spinels to improve the properties of magnesia brick. Spinels reduce the thermal expansion rate of magnesia brick, making them easier to contain in furnaces, especially rotary kilns. Spinels also improve the insulating value of magnesia brick.
Synthetic magnesia-alumina spinel is used in minerals processing applications and has displaced magnesia-chrome brick in rotary kiln applications worldwide. Chrome ore blends with magnesia have been used for 90 years in the refractory industry. Chrome raises the initial melting temperature in basic refractories and increases resistance to siliceous slags.