Rotary Kiln Calcining Zone Refractory Challenges
Articles
Part 1: Charging Zone
Part 3: Burning Zone
Part 4: Discharge Zone
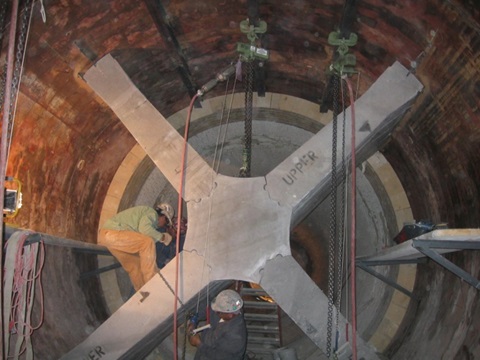
Cross-type refractory heat exchangers have either three or four legs and are fabricated from refractory castable that is heat-treated.
Calcining Zone Refractory Challenges
The calcining zone prepares the stone feed for the burning zone, where the decarbonization reaction is driven to completion. For the calcining zone lining, 70% alumina class brick refractory is most commonly used in North America. Internals are frequently located in the calcining zone, including lifters refractory heat exchangers (refractory crosses), and dams. The two former structures increase mixing within the charge, while the latter increases the residence time of the charge in the kiln. Refractory heat exchangers also absorb heat energy from the flue gas and return it to the charge by radiative and conductive heat transfer.